Understanding Pallet Rack Specifications
- Michael Whitehead
- Feb 22, 2024
- 4 min read

Pallet racks are an effective way for warehouses to enhance their storage space without needing to rely on extensive remodeling of their current building. But it’s not as simple as purchasing and installing pallet racks. It’s critical to understand pallet rack specifications before committing to any purchase.
Depending on what you must store, you may require specific racks that have certain capabilities; installing a rack that cannot withstand your stored items can result in damage and unsafe working conditions. Knowing these specifications allows you to make informed decisions that will increase your current storage space in the safest way possible.
Different Pallet Rack Types
Before you take any further steps, you must understand the various types of pallet racks.
Selective Racks
These types of racks are very basic in design, as they only utilize vertical uprights connected by horizontal load beams. The rack itself is open on the front and the back, allowing warehouse workers to access it from either direction. Due to how simple the design is, selective racks are the most common option for storage facilities.
Pallet Flow Racking
Constructed much in the same way as selective racks, pallet flow racking systems differ in that they specialize in high-density loads. The other major design difference is that pallet flow racks utilize rollers when storing pallets, as well as adhering to a first-in, first-out system. This means there is a single point of entry for the pallet, and once on the rollers, the pallets move to the exit in the order they came in.
Drive-In Racking
Drive-in racks are long, vertical systems that allow forklifts to drive up and easily place pallets on different levels. The drive-in rack utilizes a last-in, first-out method of storage, as the pallets that forklift operators place first are at the farthest end of the racking system, with new pallets placed in front of it.
Decking Options
Along with different styles of racks, there are also a variety of decking types, each serving a different purpose.
Wire Mesh Decking
Wire mesh is the most common type of decking type on the market, as it has a good balance of cost and strength. The larger opening of the mesh also facilitates good airflow and reduced weight and is ideal when trying to adhere to fire codes.
Solid Steel Decking
In contrast to wire decking, solid steel decks do not have openings for air to flow or for any item to fall through. This is beneficial if you need to store smaller items that may slip through the open mesh. It is also ideal if you need to store liquids, as the closed decking can prevent liquids from spilling through.
Perforated Steel Decking
Perforated steel decking serves as a compromise between wire mesh and solid steel; the stronger material makes it more durable, and the holes allow for reduced weight and increased airflow. The perforations are also not big enough for smaller items to easily fall through.
Load Capacity
One of the most important considerations to understand pallet rack specifications is a rack’s load capacity. The load capacity is the total weight that the rack can safely handle; the exact capacity is something that the manufacturer determines. You never want to place more weight on your pallet rack than what the manufacturer specifies, as it can result in immediate safety risks and endanger employees working nearby.
Overloading a rack can cause the supports to buckle under the weight, immediately dumping the items you stored on that rack. On top of worrying about the falling debris, the sudden failure of your rack jeopardizes the rack system as a whole. If one part of your racking system fails and breaks, it will put further stress on all nearby load beams and platforms.
Load Distribution
As mentioned, load capacity determines how much weight a pallet rack platform can support, but it also relies on proper load distribution. Even distribution on a rack is key to maintaining your rack’s structural integrity; placing too much weight on either side risks structural failure. It’s important to think of the beam columns as supporting two halves of the whole load capacity. For example, while the load capacity may be 5,000 pounds, each beam column can support 2,500 pounds.
Placing the entire 5,000-pound load on one side of the pallet rack essentially exceeds the capacity by double, risking that beam column’s failure. Always ensure even distribution and emphasize the importance of this practice during training to ensure no employee mistakenly puts too much weight on any one side of your pallet rack.
Frame Depth
The frame depth is the space between the load beam columns, which is the amount of space you have from the front of the rack to the back. The greater the depth, the further back you can push your pallets. It’s essential to understand how much depth you need before installation, as having too shallow of a depth can create serious issues. A frame depth that is too shallow for your pallets creates an unsafe amount of overhang, the length of the pallet that sits past the edge of the rack.
A little overhang isn’t necessarily a safety concern. In fact, some overhang is necessary to ensure the whole weight of your pallet does not rest on the wire decking. But the overhang limit is only about 3 inches at maximum; anything more than that, and you risk significant safety concerns.
Order The Pallet Racks You Need
Keeping pallet rack specifications in mind is critical not just for efficient storage but also to ensure worker safety. When you’re looking for pallet racks for sale, keep in mind which type would work best for your needs and how you can make the most out of your current warehouse space.
Every storage space is a little different, and those small differences are important to consider when drafting pallet rack installation plans. If you’re having trouble developing a solid plan, it may be beneficial to reach out to companies that specialize in pallet racking, as they have ample experience with specifications and installation.
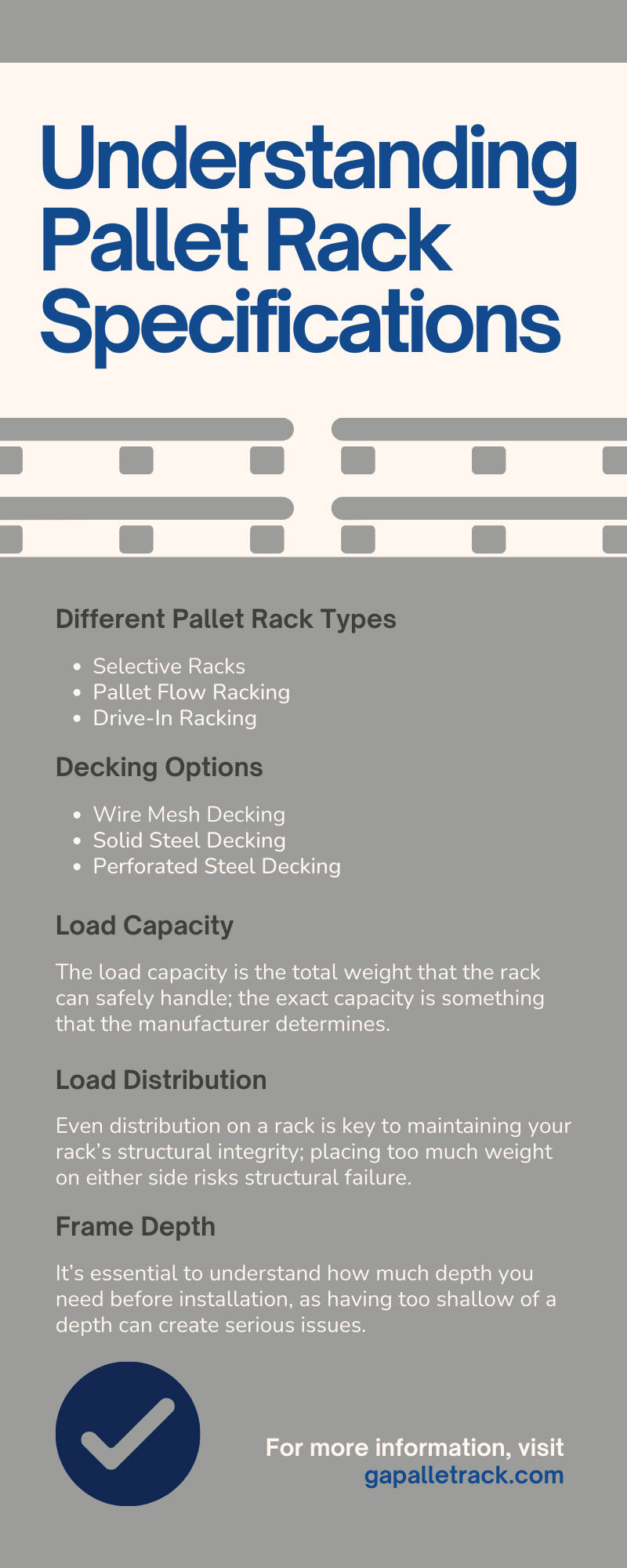
Comments